Want to know more about our support?
News
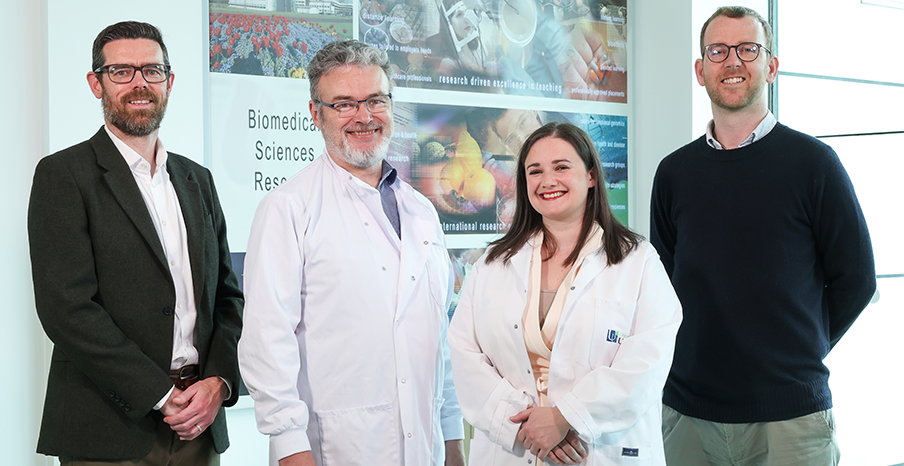
£3 million investment in Coleraine companies will improve outcomes for cancer and metabolic disease patients
25 June, 2025
Invest Northern Ireland has announced that two Coleraine SMEs are the first to receive investment from its £39 million equity fund, Co-Fund III.
Minister welcomes US trade successes
07 May, 2025
Invest Northern Ireland appoints key leadership roles
03 April, 2025
London based Napier AI to create over 100 jobs in the north
18 February, 2025
CIGA Healthcare secures £1.4m contracts in the US and Europe
17 February, 2025